Bearing Life and Effects of Harsh Operational Environments
In the previous installment we learned how bearing fatigue life is determined and the factors that can affect performance. In this second and concluding installment we will detail how harsh operating environments can negatively impact bearing life and steps that can be taken to meet the challenges these environments present.
We hope the previous installment provided you with useful information on the characteristics that influence both bearing life and load ratings. You can read Part 1 of this discussion here.
When subjected to harsh operational environments, bearing life can be greatly reduced. Design modifications are typically required to maintain life expectancy. Changes may include materials for rings and rollers, coatings, seals, retainer materials and lubricants. Before making any modifications, designers must consider all environmental factors in determining appropriate changes.
Three common and challenging operating environments that impact bearing life are high temperature, corrosive materials, and vacuum. To meet performance goals, designers must account for these conditions.
High-Temperature Environments
Custom bearings can accommodate temperatures exceeding 350°C. To design a custom bearing used in such environments, designers must consider both the bearing material and lubrication.
52100 chrome steel is a common ball and roller bearing material that can withstand temperatures up to 125°C. Heat-stabilized materials must be considered for temperatures above 350°C. Also, high-temperature grease or oil that can operate up to 285°C should be incorporated into the design.
Corrosive Environments
Water and chemicals can have a profound impact on the longevity of bearings. While rings and components are commonly made of stainless steel, consider nitrogen-enhanced martensitic stainless steel, which offers five times the corrosion resistance. Similarly, ceramic material can be used for rolling elements, which delivers exceptional performance in corrosive environments.
Vacuum Environments
Vacuum environments, including those encountered in space, impact retainers and lubricants. Trapped gasses or vapor may be released from these components (outgassing) and condense on optical elements, such as lenses, solar cells, and navigation sensors. The rate of outgassing increases at higher temperatures, requiring solid lubricants, including gold, silver, molybdenum disulfide, and polytetrafluoroethylene. Additionally, austenitic stainless steel AISI 304 is the preferred retainer material, reducing the torque between the rolling elements and the retainer.
.png)
3D CG rendering of an artificial satellite.
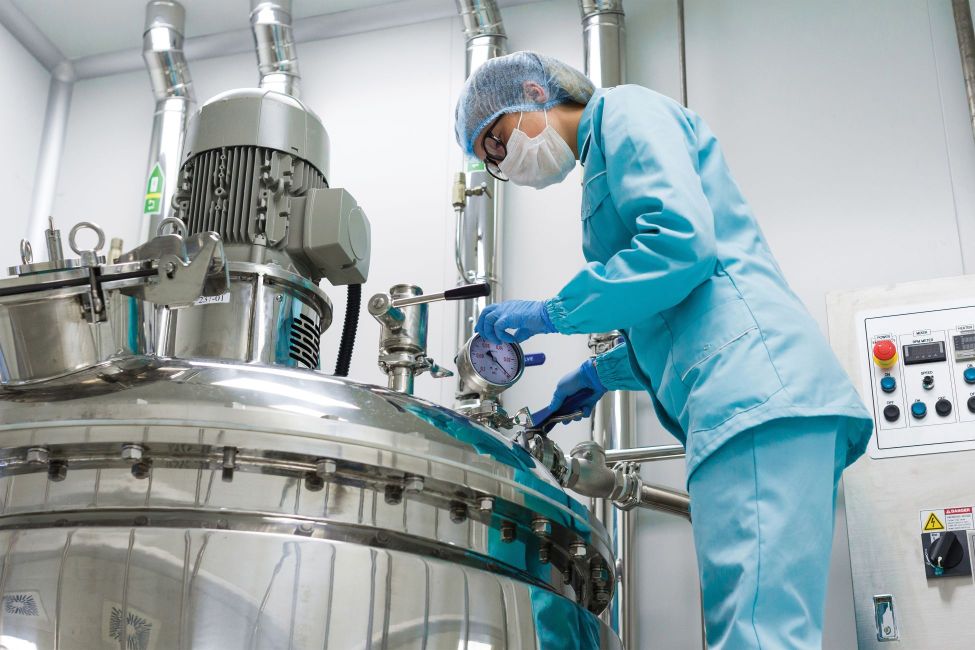
Aluminum tanks for the storage of raw materials in the chemical industry, sterile conditions in the enterprise.