Radial Ball Bearings life and load ratings
Radial Ball Bearing Life
When radial ball bearings rotate, the inner and outer rings and rolling elements are constantly loaded. This produces material fatigue and eventually bearing failure. The total number of revolutions before a failure occurs is called the basic rating life.
The bearing life of individual bearings varies considerably, even if they are of the same size, same material, same heat treatment and are under the same operating conditions.
Statistically, the total number of revolutions reached or exceeded by 90% of a sufficiently large group of apparently identical bearings before the first evidence of material fatigue occurs is called the basic rating life of a bearing.
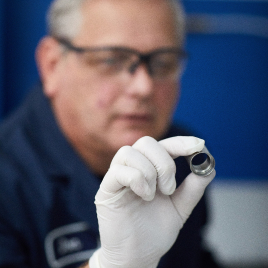

Bearings Catalog
Check out our online product catalog with more than 10,000 products with full specifications & 3D CAD Models available for download - all free of charge!
Radial Ball Bearing Load Capacity & Ratings
Manufacturers of ball bearings typically publish Load Ratings for each bearing they produce. The methods used to calculate ratings can vary from manufacturer to manufacturer. However, both ABMA and ISO have published standards related to load ratings.
- ABMA Std. 9 – Load Ratings and Fatigue Life for Ball Bearings
- ABMA Std. 12.1 and 12.2 – Instrument Ball Bearings
- ISO 76 – Static Load Ratings
- ISO 281 – Dynamic Load Ratings and Rating Life
With regard to load ratings, one thing to remember is - static load ratings (Cor) and dynamic load ratings (Cr) are formulated on completely different premises and have no direct relationship to one another.
Dynamic load ratings are determined by bearing geometry, number and size of balls, bearing pitch diameter, and ring and ball material. This load rating is used in conjunction with the actual applied radial load to calculate bearing fatigue life.
The static load rating relates to limiting loads applied to non-rotating bearings. The static load rating depends on the maximum contact stress between the balls and either of the two raceways. It is affected by material, number and size of balls, raceway curvatures, raceway depths, and contact angles. It is also based on using clean, high quality bearing steel with typical hardness levels of 58-64 HRC for rings and 60-65 HRC for balls.
Based on the above, for a given bearing, a change in the pitch circle can impact the dynamic load rating, and a change in the ball diameter or ball quantity can impact both load ratings. Changing all of these variables at the same time (depending on what the actual changes are) can result in the dynamic capacity moving in one direction and the static capacity moving in the opposite direction (when compared to the original configuration).
Radial Ball Bearings Basic Dynamic Load Rating, Cr
The basic dynamic load rating of a bearing with rotating inner ring and stationary outer ring is that load of constant magnitude and size which a sufficiently large group of apparently identical bearings can endure for a basic rating life of one million revolutions.
Bearings Basic Rating Life Formula
The equation for the basic rating life for dynamically loaded ball bearings is as follows:
L10= (Cr/P)3 X 106 (revolution)
L10,h = 16667 / n · L10 (hours)
Where:
L10 = Basic Rating Life [Revolutions]
Cr = Basic Dynamic Load Rating [N]
P = Equivalent load [N]
n = Operating Speed [rpm, revolutions per minute]
L10,h = Basic Rating Life [hours]
Examples of Rating Life L10,h Values:
OPERATING CONDITIONS | BASIC RATING LIFE L10,h |
Infrequent operation | 500 |
Short or intermittent operation. Failure has little effect on function | 4000 ~ 8,000 |
Intermittent operation. Failure has significant effect on function | 8,000 ~ 12,000 |
8 hours of non-continuous operation | 12,000 ~ 20,000 |
8 hours of continuous operation | 20,000 ~ 30,000 |
24 hours continuous operation | 40,000 ~ 60,000 |
24 hours of guaranteed trouble-free operation | 100,000 ~ 200,000 |
Adjusted Rating Life Formula
The above life formula is for general use. In cases where reliability of over 90% is required and where influences apart from load and speed or operating frequency should be taken into account for the rating life, ISO 281:1990 gives an adjusted rating life formula:
Lna= a1 x a2 x a3 x a4 x (Cr/P)3 x 106 (revolutions)
Lna,h = 16667 / n · Lna (hours)
Where:
Lna = Adjusted Rating Life [revolutions]; n: reliability, failure rate: [100-n] %
a1 = Life Adjustment Factor for Reliability
a2 = Life Adjustment Factor for Special Bearing Properties
a3 = Life Adjustment Factor for Operating Temperature
a4 = Life Adjustment Factor for Speed & Lubrication Operating Conditions
Cr = Basic Dynamic Load Rating [N]
P = Equivalent Load [N]
Lna,h = Adjusted Rating Life [hours]
n = Operating Speed [rpm]
Life Adjustment Factor for Reliability, a1
When a reliability of over 90% is required, the corresponding life adjustment factor should be selected from the following table
Reliability | 90 | 91 | 92 | 93 | 94 | 95 | 96 | 97 | 98 | 99 | 99.6 | 99.9 |
a1 | 1 | 0.92 | 0.84 | 0.77 | 0.64 | 0.62 | 0.53 | 0.44 | 0.33 | 0.21 | 0.1 | 0.037 |
Life Adjustment Factor for Reliability, a2
Improvement in manufacturing techniques for raw material and for heat treatment of components has led to an extended fatigue life for bearings. AST’s standard bearings are made from superior quality vacuum degassed steel, leading to an extended life for bearings. The basic load ratings have been established by taking this longer life into consideration. This gives an increase in the operating life in hours by a factor of 2.2, and an increase in the load carrying capacity by a factor of 1.3. These advantages result in a life adjustment factor for special bearing properties a2 value equal to 1 (a2=1). Less than ideal conditions require an a2 value less than 1.
Life Adjustment Factor for Operating Temperature, a3
At temperatures above 120⁰C [248°F], greater dimensional changes occur and the material hardness deteriorates which affects the bearing life. The life adjustment factor for operating temperature a3 can be taken from the following table:
BEARING TEMPERATURE ⁰C | 120⁰C | 150⁰C | 175⁰C | 200⁰C | 225⁰C | 250⁰C | 275⁰C | 300⁰C |
BEARING TEMPERATURE ⁰F | 248⁰F | 302⁰F | 347⁰F | 392⁰F | 437⁰F | 482⁰F | 527⁰F | 572⁰F |
TEMPERATURE FACTOR a3 | 1 | 0.9 | 0.85 | 0.75 | 0.65 | 0.6 | 0.52 | 0.45 |
Life Adjustment Factor for Speed & Lubrication Operating Conditions, a4
This is an adjustment factor to account for non-conventional speed and lubrication operating conditions. If the rotating speed is favorable (dm [mm] x n ≥ 10,000) or (dm [inch] x n ≥ 394), then a4 = 1. Under good lubrication conditions, with a permanent oil film between the rolling elements and the rings, then a4 = 1. In unfavorable speed & lubrication conditions, a4 < 1.
dm = Mean Bearing Diameter [mm or inch] = (bore + OD)/2 = (d + D)/2
n = Operating Speed [rpm]
Equivalent Dynamic Bearing Load, P
Load conditions on bearings are usually a combination of radial and axial loads. In order to establish the equivalent radial load with definite force and direction, we use the following formula:
P = X · Fr + Y · Fa
Where:
P = Equivalent Radial Load [N]
Fr = Radial Load [N or lb]
Fa = Axial Load [N or lb]
X = Radial Load Factor
Y = Axial Load Factor
Z = Number of Balls in Bearing
Dw = Ball Diameter [mm or inch]
Radial load factor and axial load factor:
Relative Axial Load |
e |
Load Ratio Comparison to e Value |
||||
Fa/(Z · Dw2) |
Fa/(Z · Dw2) |
Fa/Fr ≤ e | Fa/Fr > e | |||
[N, mm] | [lb, in] | |||||
X | Y | X | Y | |||
0.172 |
25 |
0.19 |
1 |
0 |
0.56 |
2.3 |
0.345 |
50 |
0.22 |
1 |
0 |
0.56 |
1.99 |
0.689 |
100 |
0.26 |
1 |
0 |
0.56 |
1.71 |
1.03 |
150 |
0.28 |
1 |
0 |
0.56 |
1.55 |
1.38 |
200 |
0.3 |
1 |
0 |
0.56 |
1.45 |
2.07 |
300 |
0.34 |
1 |
0 |
0.56 |
1.31 |
3.45 |
500 |
0.38 |
1 |
0 |
0.56 |
1.15 |
5.17 |
150 |
0.42 |
1 |
0 |
0.56 |
1.04 |
6.89 |
1000 |
0.44 |
1 |
0 |
0.56 |
1 |
This table applies to radial ball bearings with a bore diameter up to Ø10mm, and thin type ball bearings with a bore diameter up to Ø50 mm. Consult with AST Engineering for calculations of other bearing types.
Basic Static Load Rating, Cor
The Basic Static Load Rating applies to bearings where rotating motion does not occur or occurs only infrequently. The Basic Load Ratings and calculation methods are based on methods described in ISO 281 and in ISO Recommendations NR.76, taking into account the current level of bearing technology.
Excessive static load causes brinelling at the contact point between the rolling element and raceway. As a standard of permissible static load, the basic load rating Cor for radial bearings is specified as:
- Maximum contact pressure at the contact point between rolling element and bearing ring to be 4200 MPa and total permanent deformation of the bearing of approximately 1/10,000th of the rolling element’s diameter.
- Basic static load rating for stainless steel is 80% of that for standard bearing steel.
Bearing Safety Factor, fs
A bearing system, whether stationary or during rotational motion, could be subjected to unforeseen applied loads and inertia, such as vibrational forces, impacts, shock loading, and start-and-stop action. To ensure that an appropriate bearing size is selected, a proper safety factor must be applied. The bearing safety factor, or safety modulus fs, is the ratio of the basic static load rating Cor to the equivalent load P on the bearing.
fs = Cor / P
When the use conditions are normal operation, a safety factor of 1.0 is typical. If the bearing system may be subjected to possible shock loads, the designer may wish to increase the safety factor to 1.5. And if silent and high accuracy bearing rotation is desired, a minimum safety factor of 2.0 may be required. A high enough safety factor will prevent the permanent plastic deformation condition caused by excess load between the raceway contact areas and the rolling elements.
The load ratings, formulae, adjustment factors, table values, and other technical data contained in AST Bearings’ catalogs and website are intended to provide guidance in making bearing selections, but may not be applicable in all operating conditions. Customers must ensure that an experienced and knowledgeable design engineer performs a comprehensive analysis for their specific applications. AST Bearings assumes no liability for final bearing selections and specifications.