Good Carbs. No Carbs. High Protein. Plant Protein. Non-GMO.
There’s an increased public awareness and scrutiny of our consumption habits and choices — what’s in the foods we eat and what/where/when to eat in order to obtain optimal health and performance benefits. Some may pass as fleeting trends, while others provide practical guidance that motivates eating habits and behaviors.
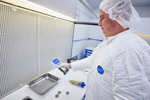
But all of these overlook an essential component of our food chain: food production. With stringent safety and hygiene requirements in effect, food manufacturers face important equipment-related decisions to ensure regulatory compliance as well as a healthy bottom-line.
Critical to the performance and productivity of a variety of food processing equipment are ball bearings. As such, designers and engineers face critical decisions when determining the specifications for ball bearings used in this equipment. These include selection of materials, lubrication type and amount, and sealing or shielding options. In most cases, these choices impact the durability and efficiency of bearings in food production applications.
Below are important concepts to consider when selecting a bearing used in food production equipment.
Regulatory compliance
Two federal food agencies provide regulatory oversight of food processing in the United States: USDA FSIS and FDA. They mandate that all materials used in food processing, including bearing lubricants, must comply with federal requirements. Additionally, the actual bearing itself may require USDA/FDA approval.
Materials
Bearings used in food production equipment must be comprised of high purity materials. While many bearings are produced from SAE 52100 chrome steel, food processing applications generally use martensitic stainless steel (similar to AISI 440C), which is corrosion resistance and offers comparable fatigue life.
For additional corrosion resistance, we recommend nitrogen-enhanced martensitic stainless steel, which offers five times the corrosion resistance of 440C type materials.
Other bearing components and their preferred composition include:
- Shields, slingers, cages: AISI 302 or 304 stainless steel
- Insert bearings in housing units: 440C stainless steel
- Housings: Consider the application — wash down solutions, high moisture environments. Each requires specific considerations. Stainless steel, special coatings, or even polymer housings are available.
Lubrication
As mentioned previously, lubricants may also be subject to regulatory requirements. The National Sanitation Foundation (NSF) has evolved globally to succeed the USDA and now oversees food-grade designations for lubricants. Currently, the “old” USDA food grade designations: H1, H2 and H3 are still recognized.
H1 lubricants are food-grade lubricants used in food-processing environments where there is the possibility of incidental food contact. H2 lubricants are food-grade lubricants used on equipment and machine parts in locations where there is no possibility of contact.
Determining whether there is a possibility of contact is difficult and many designers choose H1 over H2 and err on the side of safety.
For machines used in meat or poultry processing, “wash down” conditions subject the equipment, and bearings, to high-pressure water and anti-bacterial solutions, which can displace the grease. To counter this, greases with high water resistance properties must be used. In high-temperature applications, select lubricants that offer high-temperature oxidation stability.
Seals
Due to continuous exposure to liquids and debris, bearings must incorporate effective seals or shields to protect them and keep the lubricant intact. The most common seal material is nitrile rubber, which offers superior protection in contaminated environments compared to typical metallic shield. While increased torque is a consequence which reduces bearing speed capability, this is an acceptable tradeoff that prolongs product life. In food processing applications, Teflon and glass-reinforced PTFE seals can be used, which offer outstanding chemical resistance, high temperature capabilities and reduced torque.
For more information, read, “Bearing Design Considerations for the Food Industry,” written by AST Bearings Vice President of Operations, John Wallace.
Let our team of experts help with your bearing needs. Contact them here or learn more about our custom solutions.